The Ultimate Guide to Warehouse Optimization
Learn to optimize your warehouse operations for peak performance, serving the needs of your company and customers effectively.
Table of Contents
SECTION 1 What Is a Warehouse Optimization Assessment or Study?
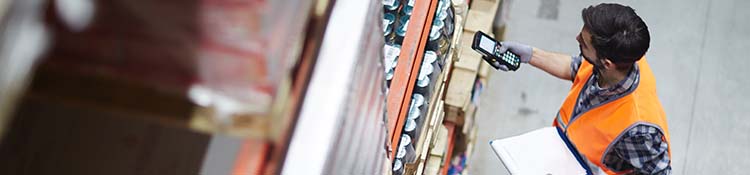
A warehouse optimization study is a disciplined and comprehensive approach to analyzing all facets of the operations. While uniqueness exist across companies, an assessment is typically going to cover all functional areas from receiving through shipping.
Additionally, optimization studies cover the warehouse layout and design as well as all inventory management functions. The goals are straightforward, you must be identifying those areas which are inefficient and drive up labor costs.
Consider those processes and bottlenecks that do not allow you to meet your management’s expectations or customer’s needs. The outputs of the assessment should be the basis for developing a roadmap for improving the operations over time.
How to Optimize Warehouse Operations
A methodical optimization assessment should take the following aspects into account:
- The product and order flow through the operations and supply chains.
- The overall utilization of the facility and storage locations.
- Material handling equipment, automation, and storage are utilized in the facility.
- The product slotting, location profiles, and management of bin locations.
- Value Added Services (VAS) such as kitting, labeling, repackaging, etc.
- Vendor compliance programs for inbound goods.
- The warehouse management software utilized in the operations.
- The inbound and outbound docks, and the staging space required.
- The organizational structure for the operations.
- Benchmarking and metrics are utilized to manage the operations.
SECTION 2 When To Consider a Warehouse Optimization Assessment
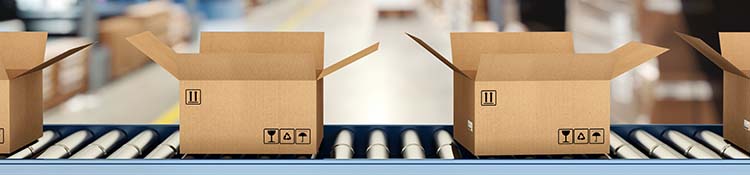
Successful operations have a mindset of continual operational improvements. This keeps problems from slowly building to the point where the operations can no longer be efficient or service the customer.
There are circumstances where businesses should look at operations holistically on a larger scale. These circumstances generally include the following:
- Decline in inventory accuracy – changes in the four-wall inventory accuracy, or bin level accuracy, are strong indicators of a breakdown in processes.
- Failure to meet customer expectations – these failures tend to stem from order accuracy issues, poor packaging, order turnaround time, etc.
- Acquiring a new business – a new acquisition generally means increased inbound shipments, more picking volumes, and additional SKUs.
- Within the final year of a lease – towards the end of a lease is when you want to analyze the operations and determine if the existing facility will continue to support your business.
- Addition of new product lines – with new product lines and SKUs comes potentially new warehouse layout optimization and system needs.
- At the end of a season – the end of a season is the perfect time to step back and look at how the operations performed overall.
- Escalating fulfillment costs – this is another indicator that points to a breakdown in processes, or inefficient labor, that should be evaluated.
SECTION 3 Reasons To Perform a Warehouse Optimization Study
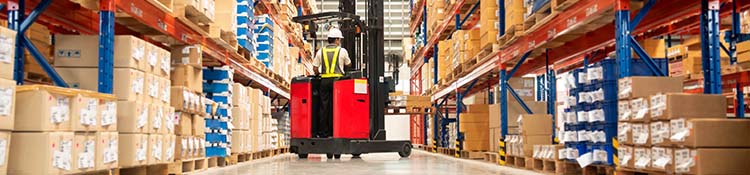
With businesses being more competitive, the need to continually improve the operations becomes more critical. A warehouse optimization assessment is a supply chain management tool that will help to identify areas that should be improved.
Faster order turnaround and accuracy - Many consumer businesses are driving towards the latest order cutoff times available with parcel carriers. For business-to-business channels, the demand is equally as stringent.
For many companies, the window for receiving and fulfilling customer orders has decreased to roughly 30 to 90 minutes. An optimization assessment will identify areas where companies can become more nimble in processing orders by identifying excessive touchpoints and bottlenecks.
Orders must be fulfilled on time and accurately. The cost of picking errors and the impact on customers must be factored into the process. Assessments also identify warehouse optimization techniques, material handling equipment or automation to support the order fulfillment process.
ERP and WMS utilization and capabilities - An optimization study will help identify gaps within the current ERP or WMS software. These gaps generally prevent a company from efficiently processing customer orders. Once the gaps are identified, decisions can be made on where and how to improve these systems.
Improve inventory accuracy – inventory accuracy tends to be one of the major challenges within supply chains. At times this can be the four wall inventory that is posing challenges. For others, the bin level accuracy becomes the problem even though the four-wall inventory is correct.
Warehouse optimization assessment will identify areas for improved cycle counting programs. However, cycle counts only clean up and correct problems once they occur. A thorough assessment will identify the root causes for how and why inventory accuracy problems arise, and effects of human error.
- Handle new SKUs or lines of business – operations are continually evolving, this includes new SKUs and product lines that are added over time, to acquisitions that are made and consolidated into the existing distribution supply chain. Warehouse slotting optimization is critical for an expanding SKU base.
These situations require operations to be flexible and scalable to support the changes over time. A warehouse optimization assessment will allow companies to determine better ways to support the existing and future SKUs.
For many companies, this will include ways to reprofile existing material handling equipment or even a redesign of the existing fulfillment operations. This can also identify opportunities for different conventional pallet racks and storage, or implementation of various levels of automation whether it be for high-density storage options or goods-to-person technologies.
- Improve processes – internally, the operations need to support efficient processes such as light assembly or kitting, to repackaging and labeling requirements. These processes are critical to supporting the needs of other departments, as well as meeting customer expectations.
These processes, if not done appropriately, will become costly from a labor perspective, as well as consume more space than needed – not to mention creating bottlenecks and potentially driving up the number of touch points.
An assessment will identify opportunities for warehouse process optimization improvements and efficiencies.
SECTION 4 Ways Companies Save Money Through Warehouse Optimization
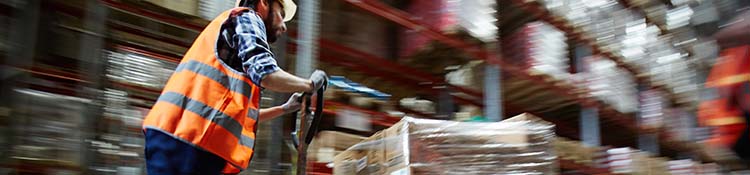
Warehouse optimization assessments are all about controlling or driving down costs as well as gaining efficiencies to handle more throughput and better service the customer – critical aspects to supply chain management. At times, this could also be about heading off future costs – such as being able to push off moving to bigger space.
These warehouse optimization solutions should be the driving factors in the continual improvement of the processes, systems, and flow in your distribution centers. The following are where most companies save money by performing a warehouse assessment.
Improved Warehouse Space Optimization – Warehouse assessments should be pointing you towards opportunities to improve both space utilization and capacity.
By finding these opportunities, companies can either hold off on having to move to a bigger space, build or rent adjacent space, minimize, or reduce offsite storage for goods.
By improving space utilization and capacity, companies typically improve the overall flow and minimize congestion.
Improved Warehouse Labor Optimization – A warehouse assessment will highlight areas where headcount can remain neutral or unchanged as volumes grow or a reduced headcount due to improved processes.
- Receiving and putaway – labor can be streamlined by finding ways to improve inbound vendor compliance and more intelligent putaway logic.
- Picking – more efficient picking, which leads to higher throughput while reducing labor costs.
- VAS – more efficient work cells and better flow of goods reduce labor costs.
- Customer return process – more efficient processing of orders.
Warehouse Automation Optimization – The use of warehouse automation is a common outcome in an assessment. Warehouse automation covers a wide range of functions and uses, reducing both space needs and labor costs. Various automation includes:
- The use of conveyors or Autonomous Mobile Robots (AMR) to move goods, reduces wasted travel time. These can support receiving putaway, return process and put away, and movement of goods between functions.
- Goods-to-person picking technologies provide high-density storage options, as well as the highest picking rates.
- Shipping automation includes print and applying weigh-in-motion scales, and carton dimensioning to reduce labor for outbound volumes and major increases in throughput.
- High-density storage including Vertical Lift Modules (VLM), AS/RS, and shuttle-based systems. These reduce space needs and can reduce labor costs.
Warehouse Inventory Management Optimization – Warehouse assessments identify ways to improve inventory management and track inventory more accurately. When inventory is more accurate it reduces the amount of capital invested in inventory, lost worker time while picking, and fewer write-offs.
- Reducing the lost time from pickers dealing with inaccurate bin locations.
- Cycle counts that find and correct errors and point to missed training opportunities in putaway and picking.
- Improved SOPs, controls, and organizational changes to reduce inventory write-offs.
HR and Training Costs – By being more efficient, and utilizing a WMS or automation that is intuitive, companies can reduce the amount of time before a worker becomes productive, but also reduces turnover and recruitment costs.
Use of Existing Software – At times, companies find that a system can do more than how it is being used, this can allow you to hold off on replacing a system. There may also be a module worth buying versus a full replacement of your warehouse system. Consider implementing worker productivity and KPIs within your system.
SECTION 5 How to Optimize Warehouse Operations
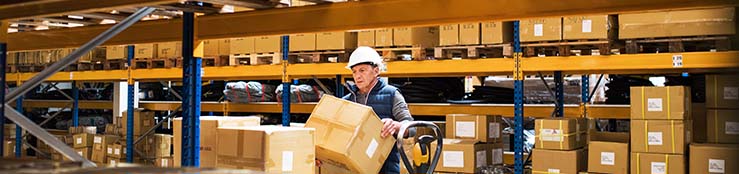
Generally, warehouse optimization studies should be conducted during non-peak volumes, preferably right after the peak season. This will provide time to develop the recommendations, implement the high-priority items, and make changes prior to the peak. There are five key aspects of how to conduct a warehouse optimization assessment, which include:
1. Observe the warehouse operations – While the bulk of the assessment is handled during non-peak times, it is recommended to be observant and documents various aspects during peak times, these would include:
- Observing the flow of goods from receiving through shipping, and documenting bottlenecks and points of congestion that need to be analyzed after the peak.
- Observing how well the stock locations are being utilized, including the use of the vertical space and height, as well as the depth, of locations.
- Noting any congestion on the receiving and shipping docks, and what is causing the congestion.
- Observe the overall pick footprint and determine if there are potential changes that should be made to reduce travel.
- Understanding what inventory management challenges arise and affect various functions such as replenishments or picking.
The goal is to observe and notate where there are problems that should be addressed. Doing this during the peak season keeps it fresh in your mind and keeps you from forgetting certain details after the peak.
2. Data gathering of necessary information and metrics – A good assessment will require a fair amount of data based on the functional area being analyzed. Some of the data to consider will include:
Order file data, many different pieces of data can be gleaned from the order file data, such as:
- The number of single line single unit orders versus multi-line orders when analyzing pick efficiency.
- The average lines and units per order for considering changes to batch picking multiple orders and other methodologies.
- The SKU velocity will help understand changes to warehouse slotting strategies and opportunities, such as wave picking or zone picking.
- Inbound receiving data to understand when and where congestion occurred, will help to understand if there are opportunities for inbound scheduling.
- Payroll and operating cost data to understand the relation of costs to order volumes and order profiles. Has the cost per order increased at a disproportionate rate to the transactional volume?
3. Interviews with key staff members – Your staff holds valuable insight as to problems that arise during peak times. The key is to filter through all the feedback and insights and determine the highest priority challenges. It is important to meet with each functional area independently. Be sure to include the day-to-day front-line workers as well as the leads and supervisors.
Start with simple questions to get the discussions going such as if you could fix three items instantly, what would they be and why? You will get a wide range of feedback, from removing bottlenecks to ergonomics which can improve morale and throughput.
4. Report analysis to determine current productivity and service levels – Along with the raw data discussed above, there are several system reports and metrics that should be available for analysis, these should include:- Worker productivity data across functions to understand how throughput and productivity performed in relation to the average lines and units per order – and against the target rates.
- Return process reason reporting and customer service reporting to understand the volume of mis-picks in the operations, this will help to identify changes in slotting, replenishment, and picking – as well as training opportunities.
5. External benchmarking to look for areas of potential improvement – from a benchmarking perspective, it is always important to understand your own relative performance, accuracy, and throughput – against yourself over time. Once you have a solid foundation, comparing yourself against external benchmarks and other companies can highlight areas of potential improvement.
It is important to understand how external benchmarks are calculated, and what data is utilized. This is critical to ensuring that it is comparable to your operations.
SECTION 6 What Should be Analyzed in a Warehouse Optimization Study
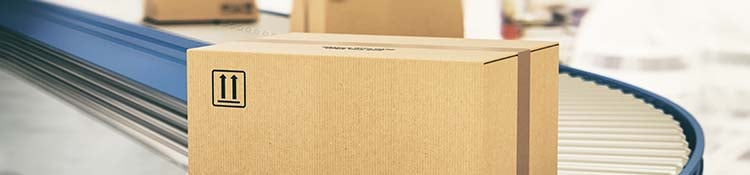
A warehouse optimization assessment initially should be a deep dive into the entire operation. Over time, as you stick to the roadmap generated, each facet can be performed regularly but at different times, not necessarily all at once, deep dive like the initial assessment. The different areas that should always be covered during your operations audit include:
The current systems and how well they support your current and future needs.
- Are there processes that need to be implemented for a new segment of business or for unexpected growth that is not supported by your system?
- Are there system modules included that you aren’t fully utilizing that should be turned on or utilized to their full extent?
The flow of goods and workers through each function within your operations. It can often be helpful to develop a flow chart during your observations that link all the directional flow of both people and product between one another.
This can help in your understanding of where bottlenecks have the potential to occur or if certain functions should be relocated to make the flow more optimal.
The use of material handling equipment (MHE) and what changes to consider.
- Should aisle widths be reduced to increase storage capacity?
- How does that affect the MHE needed to operate?
- This should also include understanding what pieces of equipment should be replaced due to higher-than-usual maintenance costs and downtimes.
Productivity reporting by process and measurement against goals.
- Is the workforce meeting the expected values?
- This is a great place to shine a light on areas that should be investigated deeper than other areas.
- Should a refresher training course be implemented to help raise the lower-than-expected productivity for a specific job function?
A measure of the current warehouse space capacity and utilization.
- Are there areas of the facility that could benefit from new or additional storage options?
- Should a reprofiling exercise occur to add more levels of storage where the cube is not fully utilized?
- How could slotting and different pick slot sizes help to increase the lifespan of the building?
- This could also have an additional benefit on the throughput of both replenishment and picking operations.
A review of Standard Operating Procedures (SOP) of each major job function and process. This is a great opportunity to review the existing SOPs to make sure that the process is still what management expects.
If you do not have SOPs, start with the job functions with the most employees (picking) to start developing first.
- Are there steps in the process that could be tweaked to improve productivity?
- How will these changes be communicated to the workforce to ensure optimal implementation?
The organization structure. Should additional supervisors on the floor team leads be developed to ensure constant visibility and understanding of the on-the-floor processes and also the culture?
Is the warehouse manager the right person to support the “big picture” items or are they too involved with day-to-day activities?
Additional Operations Resources From F. Curtis Barry & Company
As part of warehouse optimization consulting projects, F. Curtis Barry & Company helps businesses identify ways to increase efficiency while keeping their team and customers happy.
If your business is considering undergoing an optimization assessment project and you'd like expert assistance considering, planning, and navigating while doing so, we're available to help.
SHARE